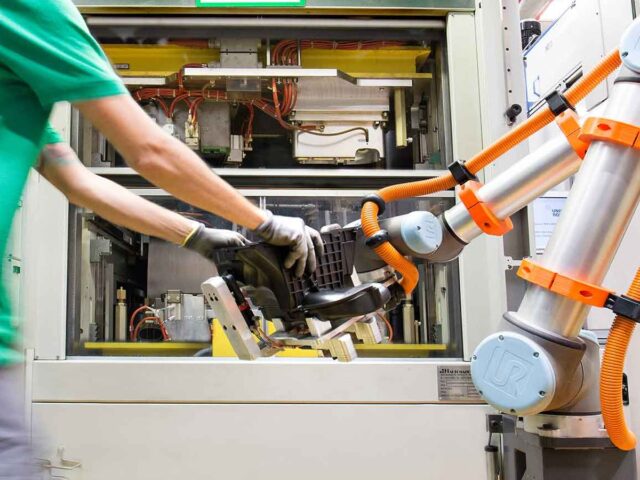
Robots were once viewed as pure science fiction and something that will live on in our everyday lives. However, modern industries rely heavily on all sorts of robotic technologies, from robot arms on assembly lines to small industrial robots that run on their own. In actuality, most branches of industry would not exist if we had to do everything by hand and through manual human labor.
For these and many other reasons, an increasing number of manufacturers around the globe are going for automation as a solution to labor shortages, low industrial productivity, safety and security, and low and inconsistent product quality. It is easy to see how beneficial robots are by simply reading about the fields they can help us with.
The introduction of small industrial robots to the market has made it easy for the manufacturing industries to quickly automate their processes, resulting in more products being made, services carried out, and revenues coming their way each new year.
Since they use them so much, these industries have become greatly reliant on the robots. This means that their productivity can only be guaranteed if the quality and state of the robots they use are optimal. Robots are machines, and just like any other machine, they ought to be subjected to regular inspection and preventive maintenance. Similarly, they can break and need replacement, which would slow down production.
In the following subheadings, we will see when and why you should regularly maintain small industrial robots. Make sure to thoroughly read the article if this sounds like something you can benefit from.
When to Perform Preventive Maintenance on the Small Industrial Robots
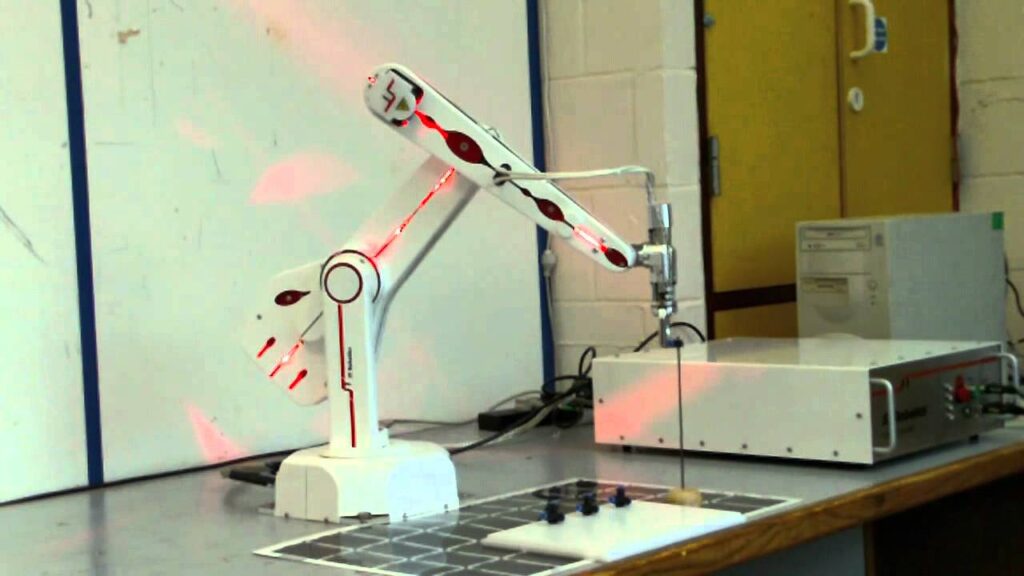
Small industrial robots can attain their optimum performance given their preventive maintenance is regular and periodic. All robots are not the same of course, hence the varying maintenance procedures and norms for the different ones. From the moment of acquisition of the robots, the maintenance kicks off and never stops until the robot works.
Robot maintenance should be as regular as after 3840 hours of operation from the previous maintenance, which comes down to 160 days or a little bit more than five months. Other manufacturers of the small industrial robots recommend one maintenance and repair instance in 12 months of the robots’ operations. This all depends on the workload and the model, but twice a year is the overall average in most factories.
Nonetheless, as a manufacturer that has invested in robotic automation for his or her processes, you must realize that the rate of maintenance of your robots will vary depending on their maintenance needs.
Carrying out the inspection as a form of maintenance is straightforward since all manufacturers make sure the crew knows how to do it. For example, the creators of Universal-Robots include a mechanical unit maintenance manual in the packaging of every robot they sell. The manual is there for a reason so always make sure that you go through it carefully so that you know how frequently you need to do checks and care for your brand new robots.
Reasons for Preventive Maintenance of Small Industrial Robots
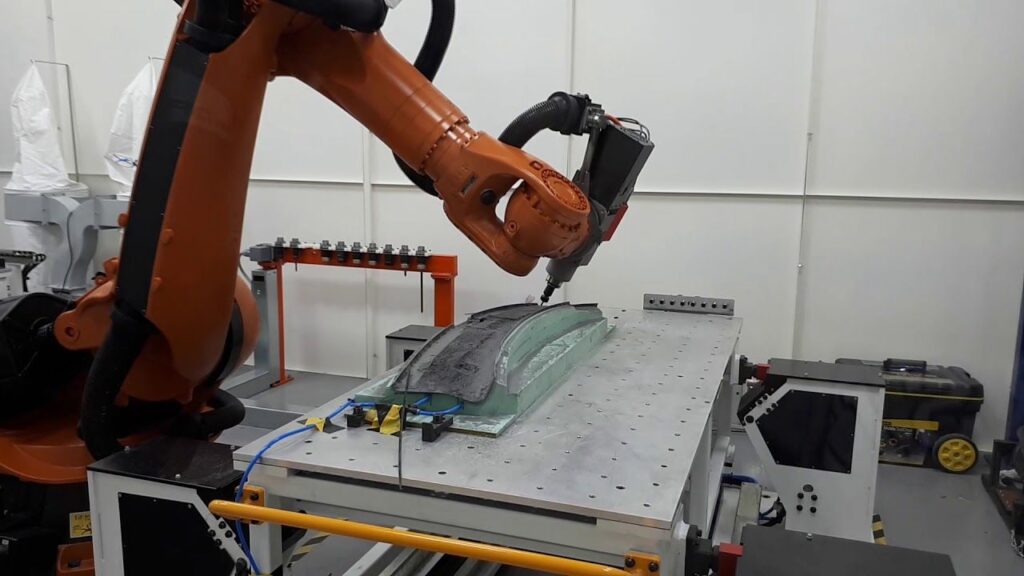
1. Increase and maintain the robots’ optimum efficiency and performance
A robot that experiences maintenance is highly efficient and performs its tasks adequately. The industries never experience any downtime in industrial operations if their robotic allies are up to speed.
2. Lengthen the robots’ lifespan
Servicing robots in a timely manner and maintaining them well will ensure they give you a long service delivery. Furthermore, the robot will remain operational to the point that the company has derived optimum benefit from it, which in turn saves money on buying new ones.
3. Ensure the safety of the staffs and other equipment
Staff and other equipment share the workstation with the robots. Therefore, if they are well taken care of, everything else will be easier to keep an eye on. Preventive maintenance of the robots ensures safety for everyone and everything else present in the workspace.
4. Prevent unexpected losses
Losses may result from unplanned shutdowns due to mechanical problems. What is more, losses may occur when there is a complete shutdown of the manufacturing plant due to the total breakdown of crucial machinery. Therefore, preventive maintenance will enable the company to avoid such losses.
Issues Arising from Non-provision of Preventive Maintenance
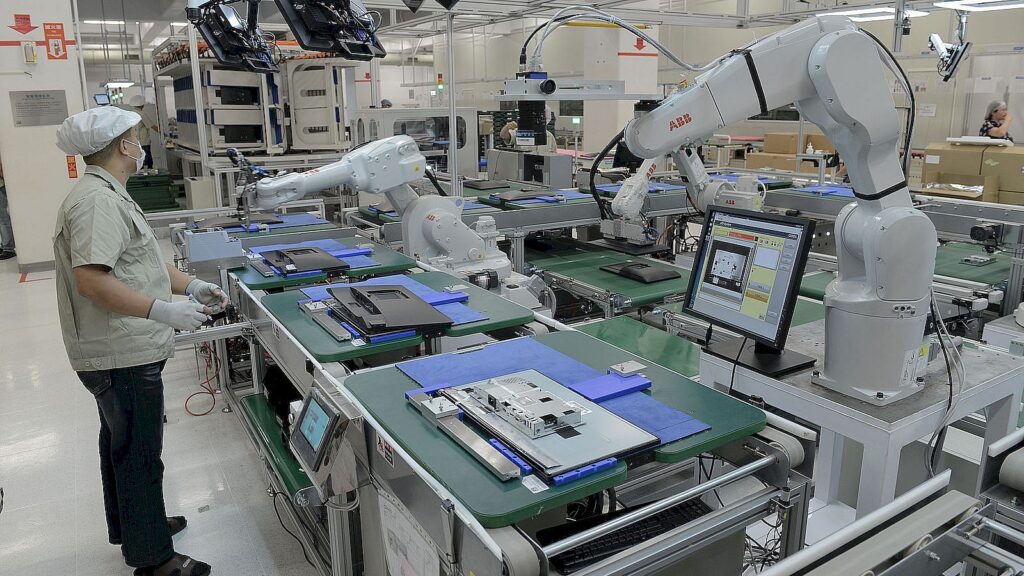
Failure to care for and provide the necessary maintenance to these neat machines will result in their inefficiency and then, of course, serious losses for your company. The following issues may arise when you fail to provide preventive maintenance to the key elements of your industry:
1. Programs’ Loss
Prolonged usage of robots without performing the mandatory maintenance procedures may result in the complete breakdown of their software, which will surely lead to the disruption of the company’s manufacturing processes. Software issues most often result in behavior issues since the machine no longer has its “brain” in order.
2. Safety issues
The breakdown of a small industrial robot hampers with their predictability. Thus, they expose employees to harm a faulty entity that can disconnect or behave abnormally and injure the staff operating them if it is not maintained.
3. Position deviation
Robots are programmed and are fitted with the specifications they are should be operating. However, when they malfunction due to delayed maintenance, they begin to operate outside the set limits and interfere with other surrounding processes.
4. Repeatability problems
One feature that makes them efficient is their ability to perform a task in repeated movements without asking any questions or getting tired. However, a prolonged lack of maintenance and care for them will lead to their malfunctioning, which in turn hinders their repeatability. And what is the point of only doing the task a few times?
5. Cable damage
Robots get used up and worn out in much the same way tools put to use experience wear and tear. Exposure and continued use of the robots result in wear and tear, which necessitates urgent replacement of the cables and other replacement parts. Failure to do so exposes the robot to a complete breakdown eventually.
Conclusion and Takeaways
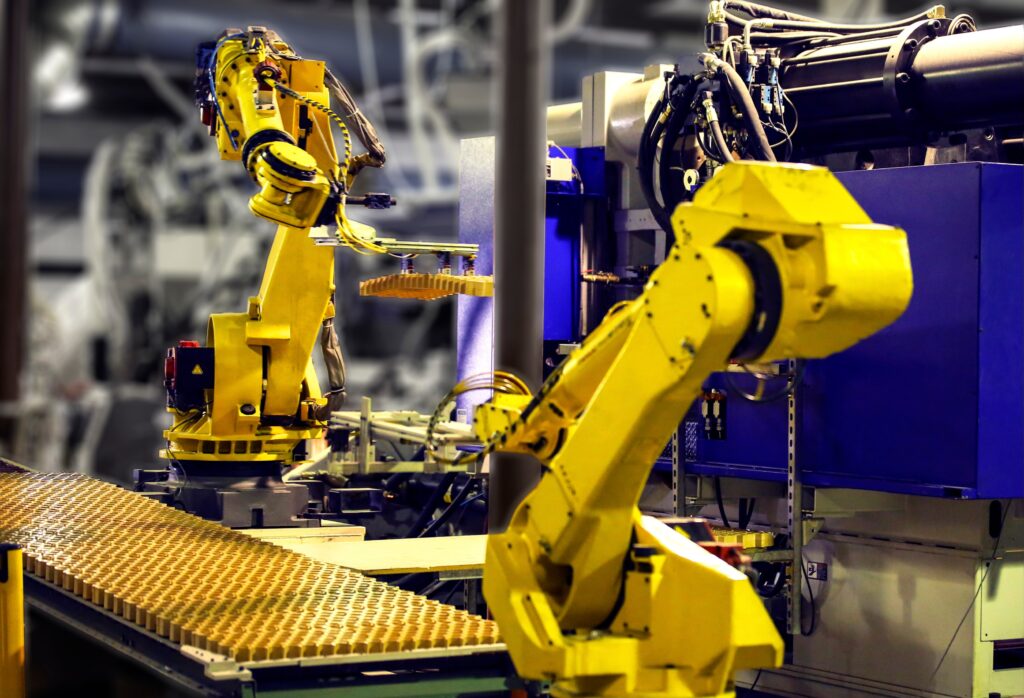
Small industrial robots are exceedingly efficient and provide optimum benefits to industries. However, that is only possible if manufacturers perform proper and timely preventive maintenance on the robots. Failure to correctly maintain them may lead to industrial losses. Hence the need for manufacturers to carry out regular and timely checks and maintenance on the robots, to guarantee the efficiency of their operations.