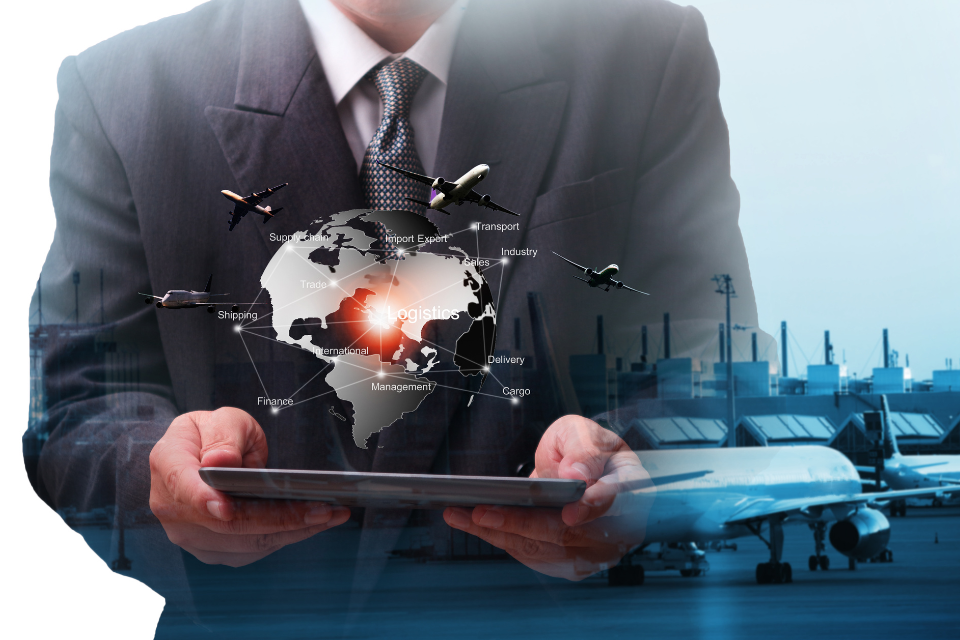
So, imagine you’ve just scored a backstage pass to the rock concert of the supply chain world. You’re there to meet none other than the band manager, but in our case, it’s the Logistics Manager.
We sat down with Jamie, a seasoned Logistics Manager with over a decade of steering shipments through the stormy seas of supply chain management. Jamie’s job is to make sure that everything your heart desires (or just the stuff you bought online last night) arrives on your doorstep right on time.
What Exactly Does a Logistics Manager Do?
Jamie breaks it down for us. “Think of it like being a puppeteer,” she explains, “except, instead of puppets, I have trucks, planes, and cargo ships, and instead of strings, it’s a whole lot of phone calls, software tools, and caffeine.”
A Logistics Manager, like Wismo, oversees the journey of products from suppliers to warehouses, and from these storage hubs right to where they need to be — which could be a retail store, a warehouse, or your house.
They plan, implement, and control the efficient, effective forward, and reverse flow and storage of goods, services, and related information between the point of origin and the point of consumption to meet customers’ requirements.
The Chaos of Coordination
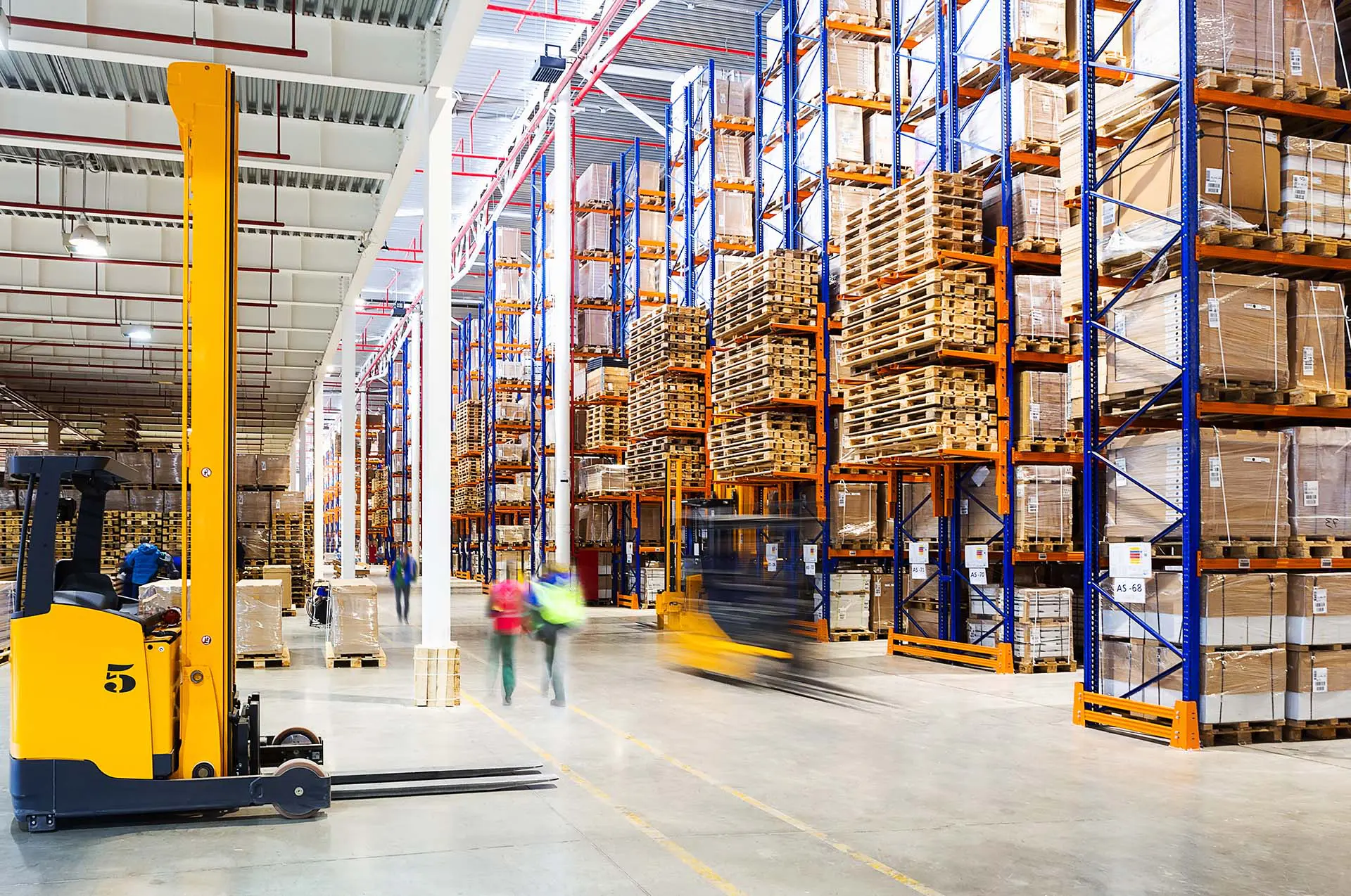
“Every day is like solving a new puzzle, but you don’t get to see the picture on the box,” Jamie says with a laugh. Handling unexpected delays, juggling transportation schedules, and managing warehouse inventories are just a slice of the daily chaos. For Jamie, the key is flexibility mixed with a solid strategy.
“You have to be ready to reroute a shipment or adjust plans at a moment’s notice. Weather delays, traffic jams, even political issues can throw wrenches in your well-oiled machine.”
Tech to the Rescue
Thank goodness for technology, right? Jamie nods enthusiastically. “Absolutely! Modern logistics is as much about IT as it is about moving boxes.” She uses advanced software that helps track every item in real-time as it moves across the globe.
This tech not only tracks goods but also predicts delays and automates responses to common issues. “For example, if a truck is delayed, the system can automatically notify the customer and rearrange delivery schedules without me having to lift a finger.”
People ─ The Real MVPs
Despite all the tech talk, Jamie insists that her team is her most valuable asset. “Tech is great, but logistics is fundamentally a people business.” Building relationships with everyone from the warehouse staff to the senior executives of shipping companies is crucial.
“You have to understand what motivates people, how to encourage them, and yes, sometimes how to light a fire under them to get things moving.”
The Customer Is Always Watching
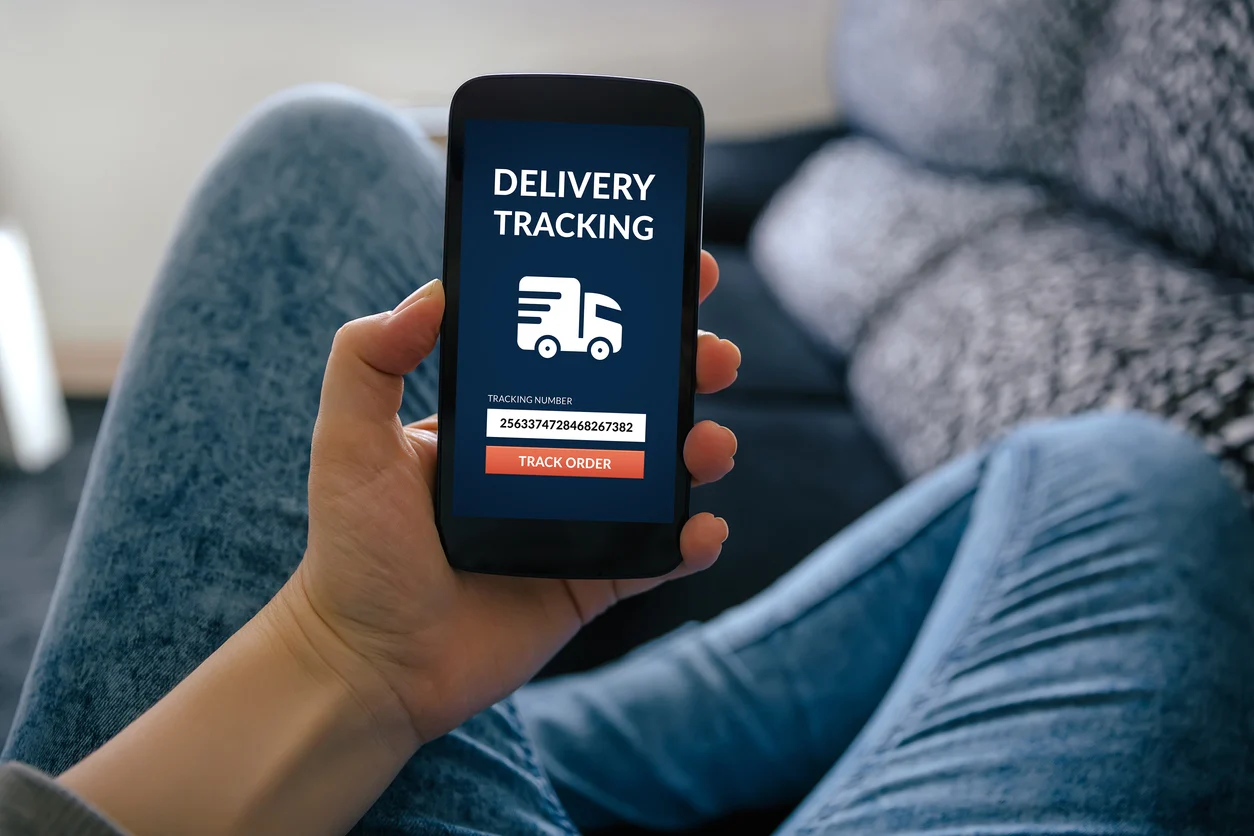
We’ve all been there, tracking our packages online, getting frustrated if there’s a delay. Jamie knows this all too well. “In today’s world, customers expect to know where their order is at every second.”
This visibility makes logistics a high-stakes game of expectations management. Jamie spends a lot of her time ensuring that these expectations are met or, ideally, exceeded. “It’s about keeping everyone in the loop and managing situations before they become problems.”
Tales from the Trenches
Jamie shared a story that sounded more like a blockbuster movie plot than a day at the office. “There was this one time we had a container of electronics that was misrouted due to a labeling error. It ended up on the wrong continent!”
She tells about the scramble to retrieve the container, dealing with customs issues, and rerouting it to the correct destination. “It was stressful, but solving crises like this is what keeps my job exciting.”
Navigating Global Challenges
Just when you think you’ve gotten a handle on things, the world throws a curveball—or in Jamie’s world, several curveballs. Global events can turn logistics into a wild ride. “You have economic sanctions, natural disasters, pandemics—you name it, it impacts us.” Jamie explains how staying informed and proactive is crucial.
“We always need to have contingency plans. For instance, when a key shipping route is blocked or there’s a sudden tariff change, we need to quickly reassess and adapt our routes or costs.”
Sustainability is Key
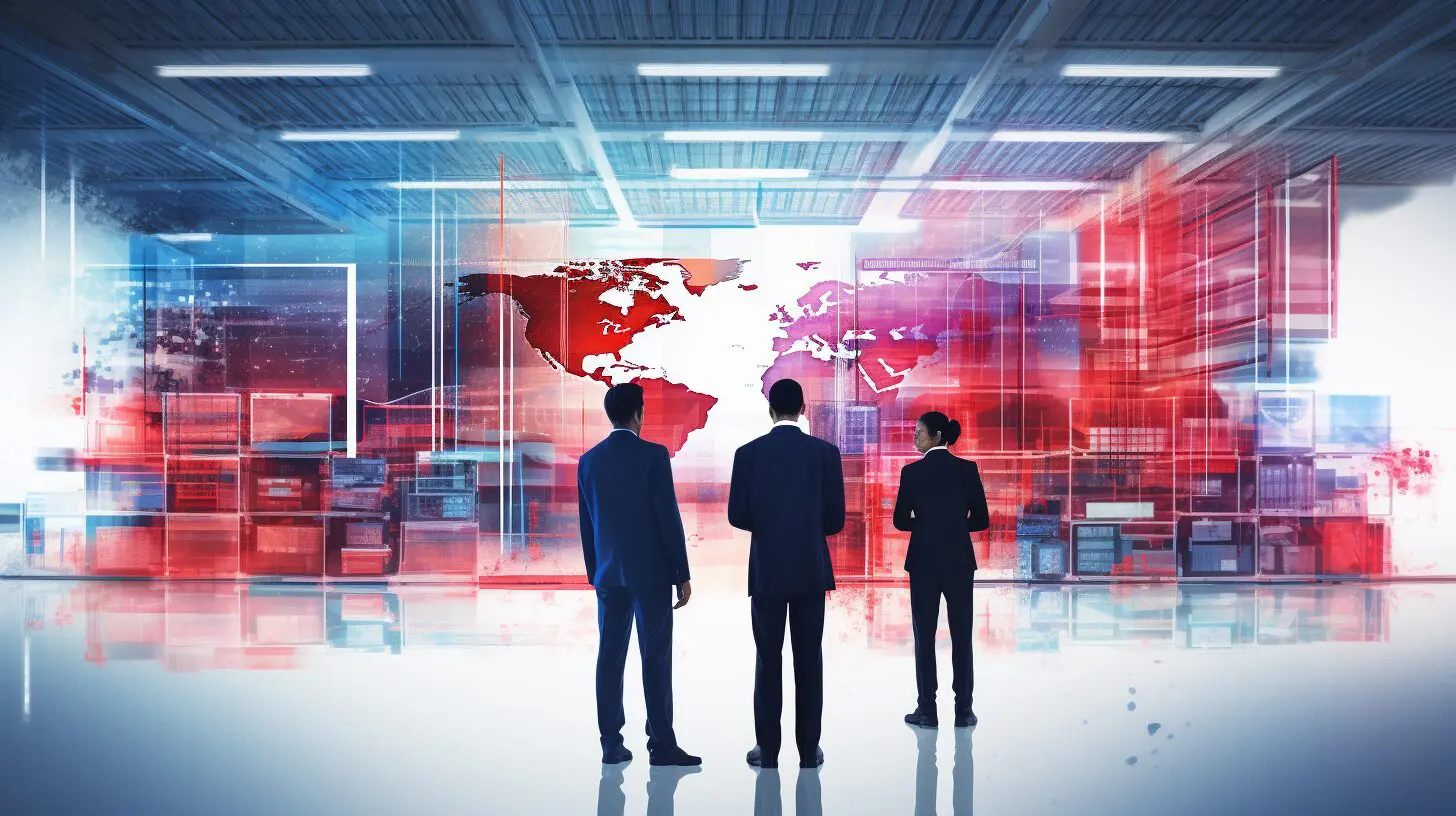
In recent years, sustainability has moved from a nice-to-have to a must-have in logistics. Jamie is passionate about this shift. “It’s not just about reducing costs anymore; it’s about reducing carbon footprints.”
She dives into how her company has started using more fuel-efficient vehicles and is exploring the use of electric trucks and drones for last-mile deliveries. “Every little bit helps, and our clients really value our commitment to sustainability.”
The Art of Communication
A big part of Jamie’s role is communication. Whether it’s negotiating contracts with suppliers, updating clients on their shipment statuses, or leading her team through a busy holiday rush, effective communication is vital. “You have to be clear, concise, and honest—especially when things go wrong,” she advises.
Keeping everyone from suppliers to customers informed not only helps in managing expectations but also builds trust and reliability.
Learning Never Stops
For those aspiring to become logistics managers, Jamie stresses the importance of continual learning. “This field is always evolving, and what worked yesterday might not work tomorrow.”
She highlights how she keeps up with the latest industry trends through courses, workshops, and conferences. “You have to be a lifelong learner to stay ahead in this game. Understanding the latest regulations, technology, and strategies is essential.”
A Day in the Life
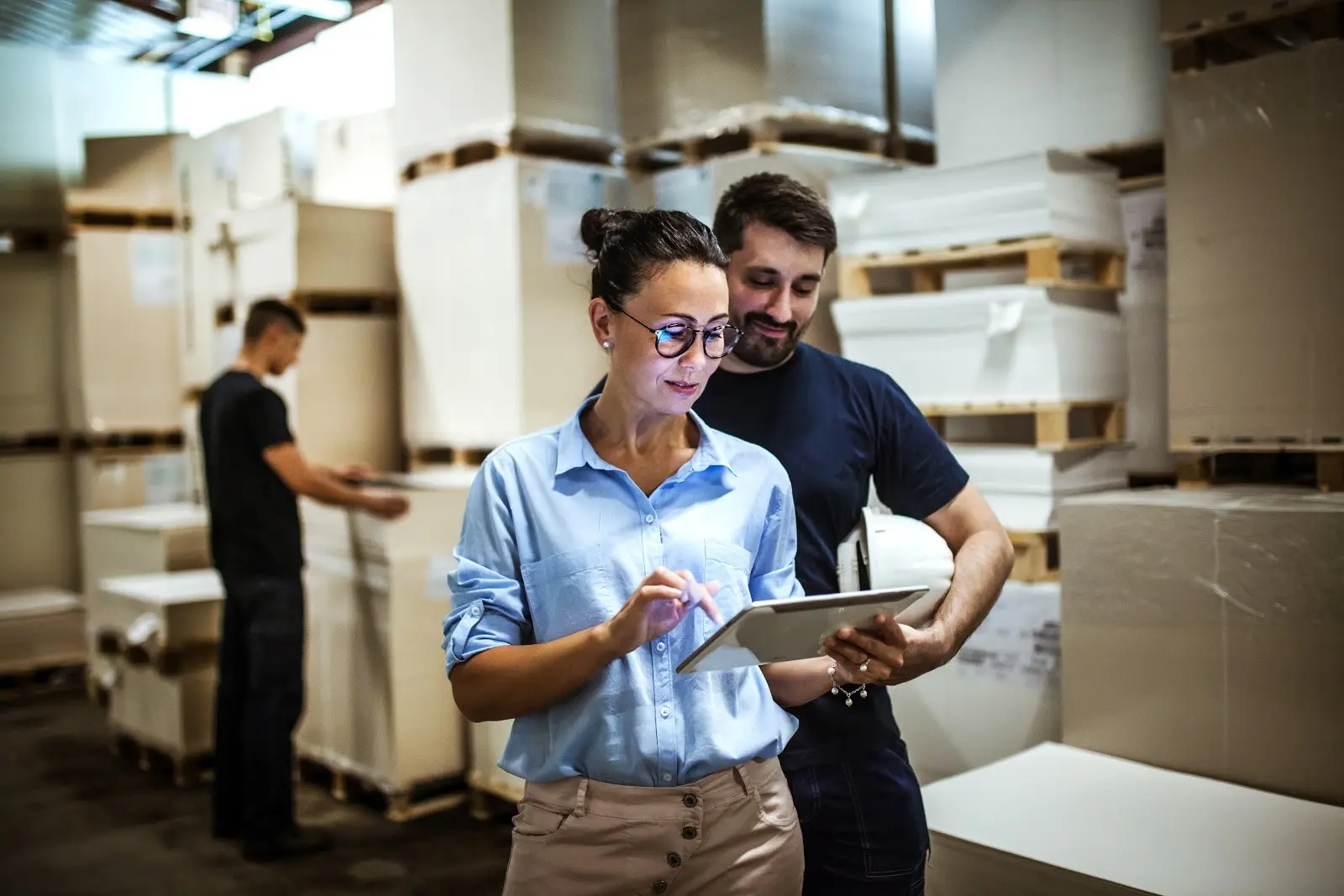
To give a real sense of her role, Jamie walks us through a typical day. It starts with checking overnight messages for any urgent issues, followed by a team meeting to set the day’s priorities.
“Then I’m on calls with suppliers or clients, solving problems, or sometimes out in the field.” She might visit a warehouse to troubleshoot a process or meet with a tech provider to discuss new software integrations. “No two days are the same, and that’s what I love about it.”