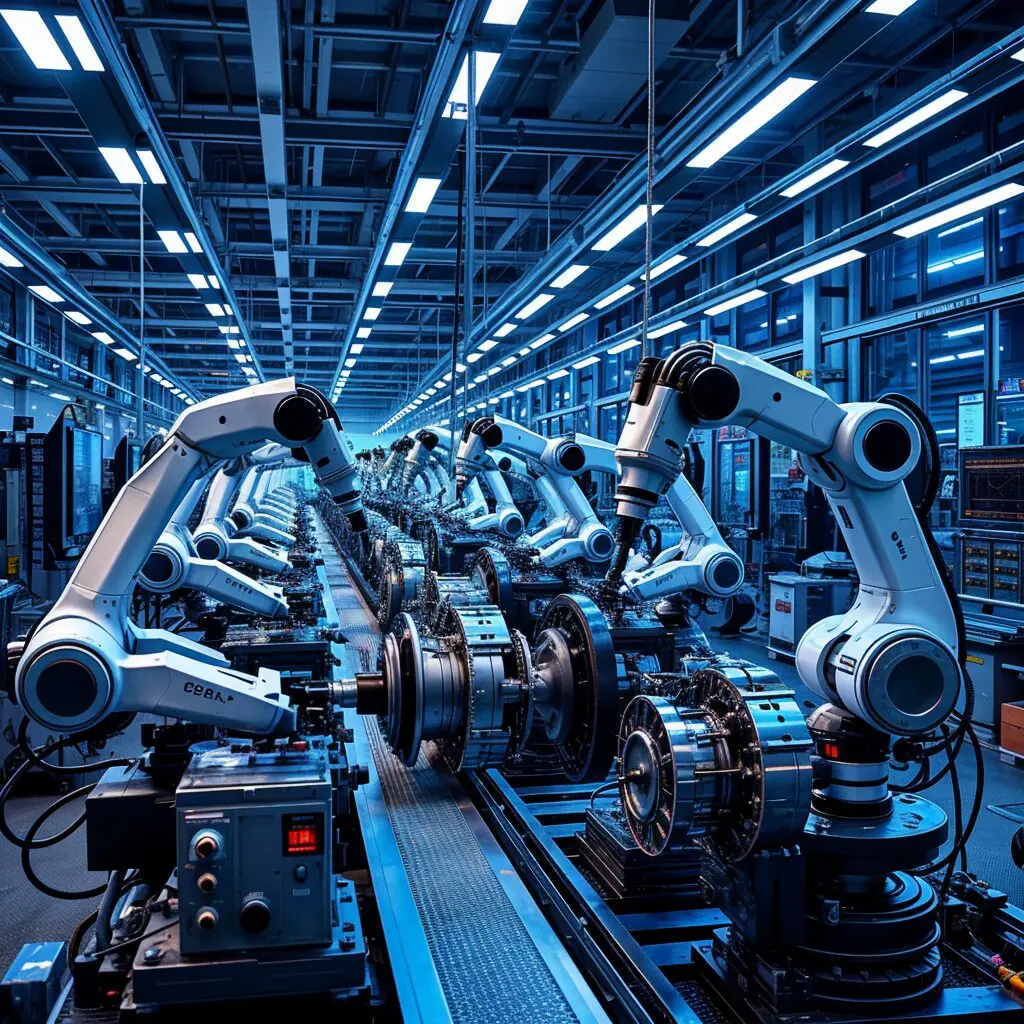
The manufacturing industry in the United States has a long and storied history, evolving from the early days of industrialization to the modern era of automation. However, the landscape of manufacturing is changing rapidly. Faced with challenges like labor shortages, rising operational costs, and increasing global competition, US manufacturers are turning to advanced technologies to stay competitive. Among these technologies, assembly robots are playing a crucial role in transforming production lines across the country.
How Assembly Robots are Revolutionizing Production Lines
One of the most significant impacts of factory robots used in assembling is their ability to enhance efficiency and productivity on production lines. Robots can operate 24/7 without fatigue, leading to a substantial reduction in cycle times and increased throughput. They execute tasks with precision and consistency, minimizing errors that can occur in human-operated processes. For example, in electronics manufacturing, robots can place tiny components onto circuit boards with unmatched accuracy, ensuring high-quality assembly at a rapid pace.
While the initial investment in robotics can be high, the long-term savings often justify the expense. Robots reduce operational costs by increasing efficiency, reducing waste, and minimizing downtime. Over time, the return on investment (ROI) for companies adopting robotics can be significant. For small and medium-sized enterprises (SMEs), financing options and leasing programs can make robotic solutions more accessible, helping them stay competitive in an increasingly automated industry.
Technological Advancements Driving the Adoption of Assembly Robots
Robotics hardware has also seen significant advancements. Modern robots are equipped with advanced sensors that allow them to “see” and “feel” their environment, making them more adaptable to different tasks. Grippers and end-effectors have become more sophisticated, enabling robots to handle delicate objects with precision.
Additionally, the rise of 5G and the Internet of Things (IoT) is enhancing connectivity between robots and other manufacturing systems, allowing for seamless communication and real-time data exchange.
Gone are the days when programming robots required extensive coding knowledge. Today, user-friendly interfaces and low-code/no-code platforms are making it easier for manufacturers to deploy and operate robots. These platforms allow operators to program robots using drag-and-drop interfaces or simple visual tools, reducing the learning curve and enabling faster deployment.
Impact on the US Manufacturing Sector
Assembly robots are playing a crucial role in maintaining the competitiveness of US manufacturers on the global stage. By automating repetitive and high-precision tasks, robots help reduce production costs and improve product quality. This, in turn, enables US companies to compete more effectively with international manufacturers, particularly those in countries with lower labor costs. Additionally, the increased efficiency provided by robots is encouraging the reshoring of production, bringing manufacturing jobs back to the US.
While the rise of robotics in manufacturing has sparked concerns about job displacement, the reality is more nuanced. Rather than eliminating jobs, robots are transforming the workforce by shifting human roles to higher-value tasks.
As robots take over mundane and repetitive tasks, workers can focus on more complex and creative aspects of production. This shift is also creating new career opportunities in robotics programming, maintenance, and systems integration, areas where demand for skilled workers is growing.
Sustainability is a growing concern in the manufacturing industry, and assembly robots are contributing to more sustainable practices. Robots operate with high precision, reducing waste and minimizing the use of raw materials. They also contribute to energy efficiency by optimizing production processes and reducing the need for rework. As a result, companies using robotics can reduce their environmental footprint while improving their bottom line.
Challenges and Considerations in Adopting Assembly Robots
The cost of purchasing and implementing robotics can be a significant barrier for many manufacturers, particularly SMEs. While large corporations may have the capital to invest in state-of-the-art robotic systems, smaller companies often struggle with the upfront costs. However, the long-term benefits, including increased efficiency and reduced operational costs, often outweigh the initial investment. For SMEs, exploring financing options, such as leasing or robotics-as-a-service (RaaS) models, can make adoption more feasible.
Technical Integration and Maintenance
Integrating robots into existing production lines can be technically challenging, particularly in facilities with outdated equipment or processes. Successful implementation requires careful planning, including compatibility assessments and potential upgrades to existing systems. Additionally, maintaining and troubleshooting robotic systems requires specialized knowledge, which may necessitate training for existing staff or hiring new talent with the necessary expertise.
Cybersecurity Concerns
As production lines become more connected through robotics, AI, and IoT, cybersecurity risks also increase. Connected robots are vulnerable to cyberattacks, which can disrupt operations or compromise sensitive data. Manufacturers must prioritize cybersecurity by implementing robust protection measures, such as encryption, firewalls, and regular security audits, to safeguard their operations against potential threats.
Conclusion
Assembly robots are revolutionizing production lines across the United States, offering a path forward for an industry facing significant challenges. By enhancing efficiency, addressing labor shortages, and enabling new levels of precision and sustainability, these robots are reshaping the future of manufacturing.
As technology continues to advance, the role of robotics in production will only grow, driving the US manufacturing sector toward greater global competitiveness and innovation. Embracing this future will require manufacturers to balance technology with human ingenuity, creating a workforce and production environment that leverages the best of both worlds.