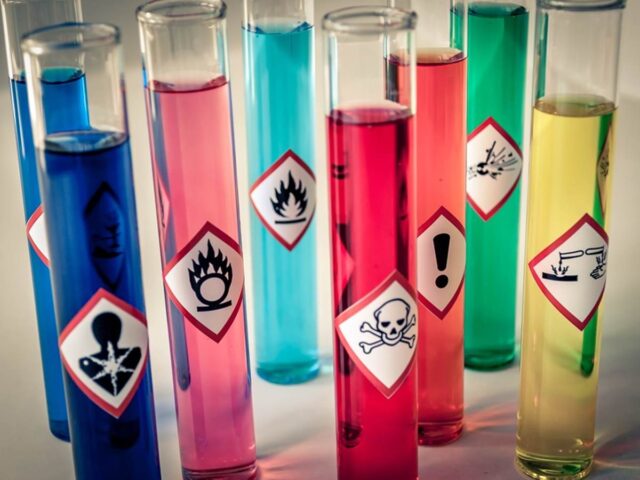
It is very important to update your SDS sheets at regular intervals, and these sheets must be duly communicated to the employees to ensure safety protocols and procedures to avoid any accidental hazards on the site. Also, employers must ensure that workers are well aware of these regulations and standards and work accordingly.
Updating and maintaining safety data sheets can be an extra burden for the manufacturer, and it is also a distraction from focusing on the core business operations. Click here to get professional services on maintaining and updating your safety data sheets with complete accuracy of the information on every single hazardous chemical.
Signs To Look For To Update Your SDS Sheets
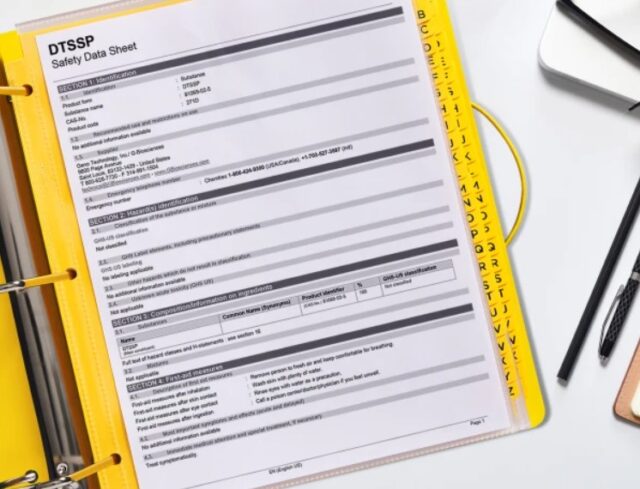
1. Discovery in hazard identification
There are all kinds of hazardous chemicals mentioned in section 2 in the safety data sheets. You might have to revise your SDS if there are any discoveries in hazard identification. Discovery in hazard identification can be related to any new classification of hazard.
Any updates in statements that may help to understand quicker and easier identification of the hazard caused due to chemicals should be updated in SDS. Also, precautionary statements and description of any new classification of hazard from a specific chemical has to be mentioned or updated in the sheet.
2. Change in composition of ingredients
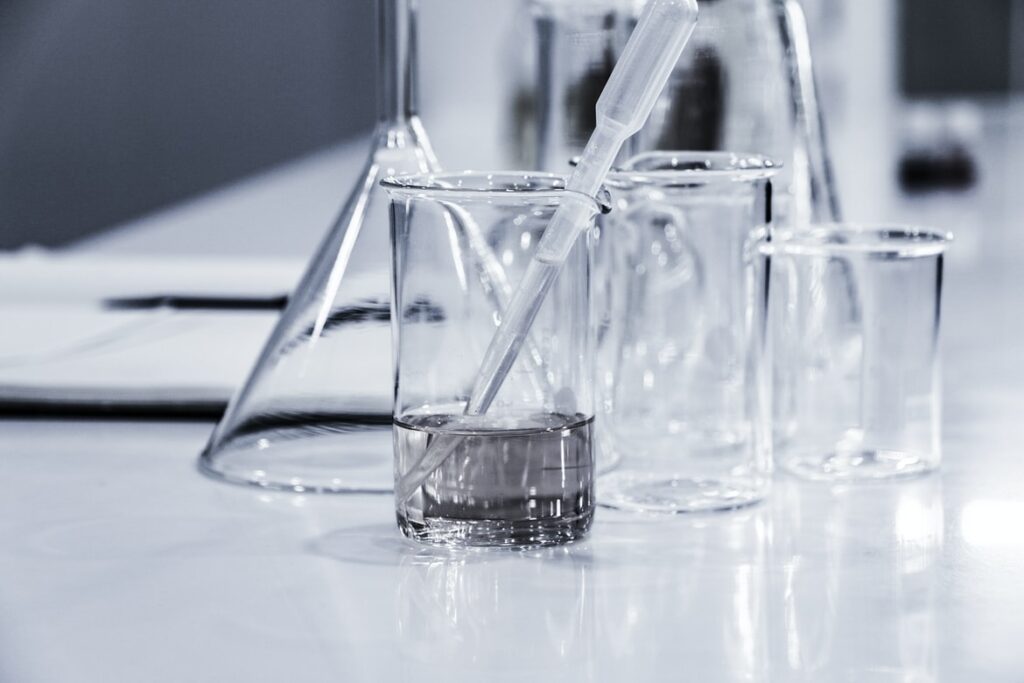
The next thing you need to update on your SDS sheets is the composition of ingredients contained in a product. Even changes in impurities and stabilizing additives related to the product must be updated. You must revise the safety data sheets even if there is any change in substance like its chemical name, Chemical Abstracts Service (CAS) and any other specific identifiers that contribute to the composition of ingredients of a product. The sheets must be revised with the exact percentage of all ingredients regarding the composition of a product.
3. New procedures for first aid measures
Any new procedures for first aid measures during any accident from exposure to hazardous chemicals must be updated in your SDS sheets. First-aid measures include the initial care that must be given to an individual if they are exposed to such hazardous chemicals.
Any new procedures to this initial treatment that can provide better care to the individual must be replaced with the old procedures. Also, any new symptoms or effects from working around these chemicals should be posted in these safety data sheets. Any new recommendations must be conveyed to the employee-related to first aid treatment and special procedures if required during emergencies.
4. New procedures for fire fighting measures
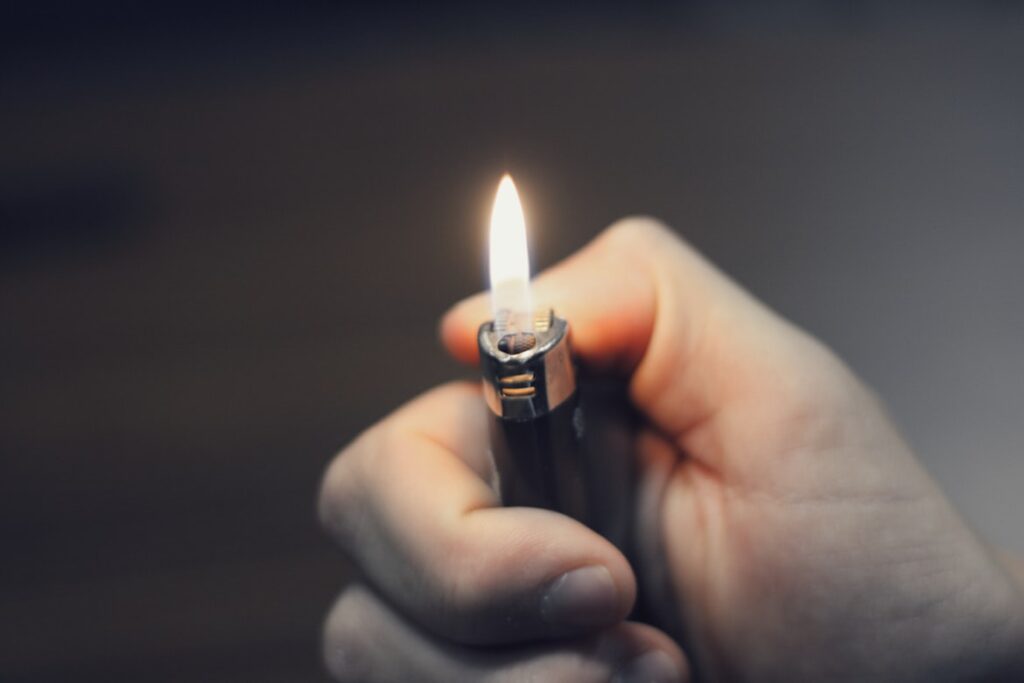
There are constant changes in new procedures in fighting a fire caused by these hazardous chemicals. As technology advances, with the help of the latest equipment and new solutions to handling these hazardous incidents must be replaced in your SDS periodically so workers can tackle any on-site accidents caused by improper handling of chemicals.
Recommendations in using the latest equipment in extinguishing the fire and safety manuals to use them effectively must be made aware to the workers through SDS. Employers must ensure that there is the availability of the latest equipment to take fire fighting measures on the site of holding the chemicals.
5. Changes in procedures to address accidental release measures
If there is any change or update in procedures on handling accidental release measures of these hazardous chemicals, it must be communicated with the employees through SDS. Employees must be provided with proper guides so they can effectively respond to any kind of accidental release measures like spills or leaks.
Also, appropriate containment and clean-up training so they don’t harm themselves and keep themselves safe from chemical exposure. Updates on information related to the change in identification of each substance must be made periodically so workers can easily distinguish between them and handle any accidental release measures efficiently.
Also, a revised version of SDS must be provided if there is any change in norms regarding safety norms and precautionary measures to address accidental release, leaks, spills of chemicals.
6. Revised procedures and guidelines on handling and storage
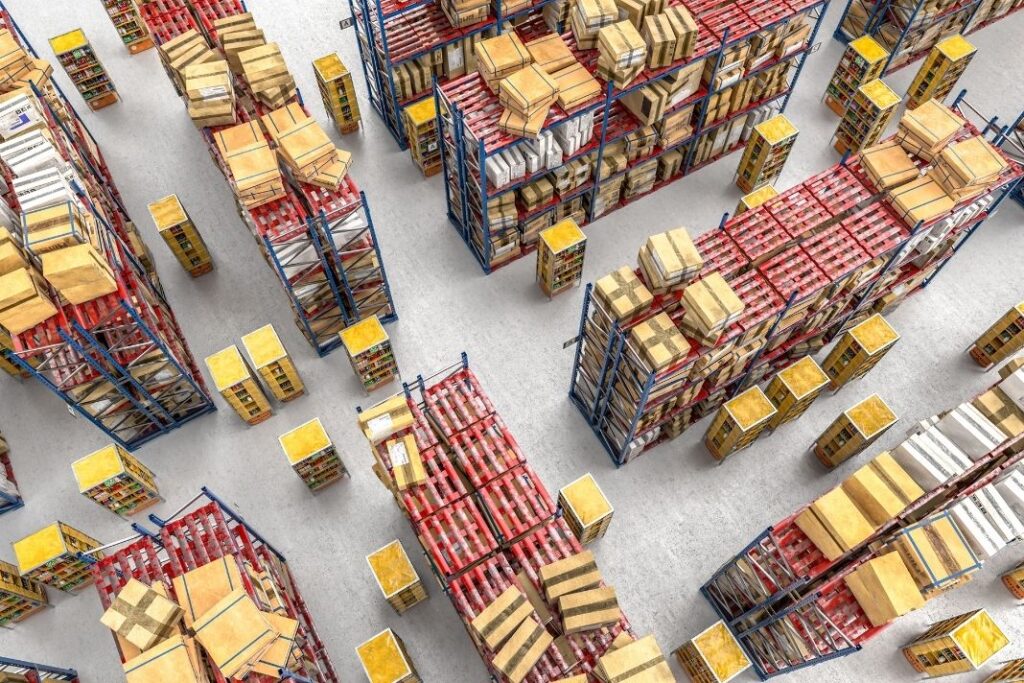
Employers must provide revised procedures and guidelines on handling and storage for every specific hazardous chemical in the updated SDS. Employers must also ensure that employees are following these procedures for safe handling and storage. Recommendations on general hygiene standards must be maintained on the site.
Updated guidelines on precautions and safe handling and storage must be well communicated to the workers to avoid any accidental release, spills or leaks. You must also revise your safety data sheets if current storage requirements are not up to the regulations, and employees are facing any kind of incompatibilities.
7. Revised procedures on exposure controls and protective measures
It’s time to update your safety data sheets with revised procedures on exposure controls and protective measures if there is any change in regulations specified by the Occupational Safety and Health Administration (OSHA). Employers must make sure that employees are working as per regulations to control any chemical exposure to the environment.
Also, workers must be communicated with the latest protective measures provided by the OSHA, and they must be equipped with personal protective equipment for personal protection during the handling and storing of chemicals.
8. Changes in toxicological information
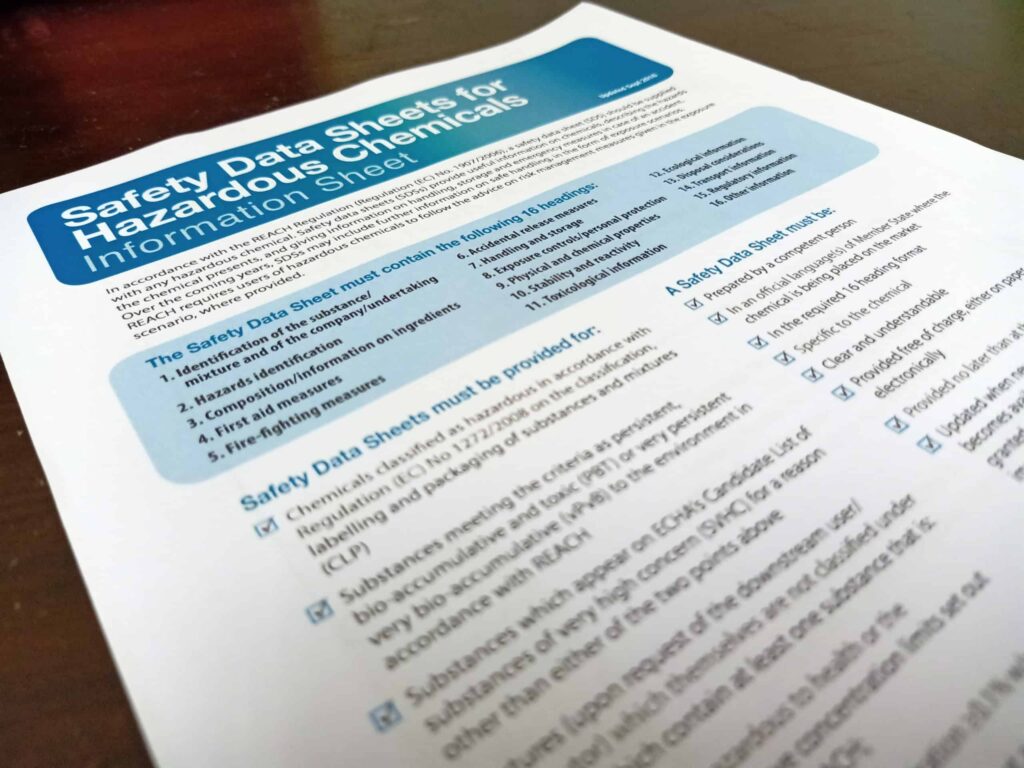
If the manufacturer identifies any signs of change in toxicological information, the same must be communicated with the employees and end-users, and they must be made aware of the health effects of working in such an environment.
It is the responsibility of the employer to update the SDS sheets, so employees are provided with every information regarding the risk of working in such an environment. Any changes in information regarding revised causes and symptoms from short term and long term exposure to these hazardous chemicals must be updated in the safety data sheets.
The Bottom-line
Safety Data Sheets must be updated by the manufacturer/ supplier within 90 days of discovering any changes related to every specific chemical and regulations specified by OSHA. Employers must ensure that the latest revised SDS are issued to the workers. These are a few common signs that you must look for to update your SDS sheets.