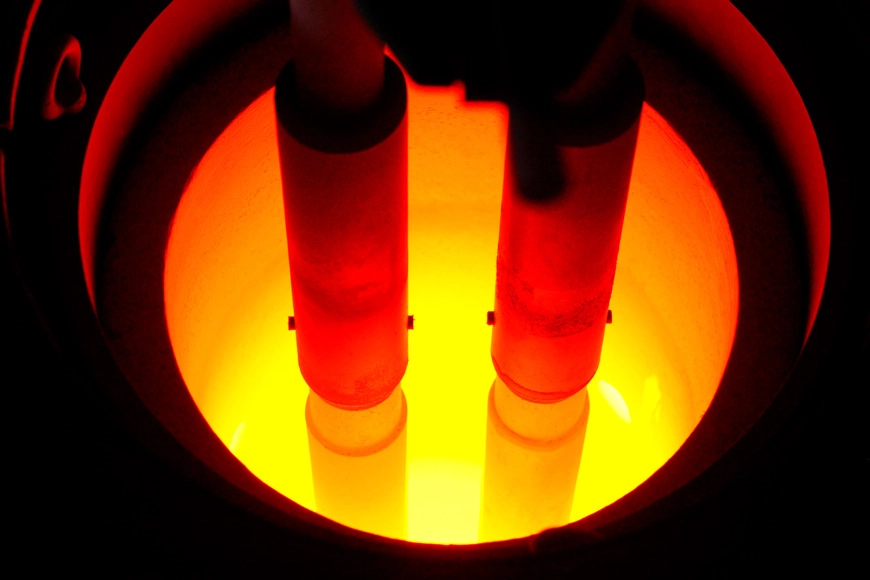
The needed heat to attain the melting point of the metal is applied to it by furnaces in metal casting. In the early phases of the metallurgical process, metals are melted in a furnace. In casting, many types of melting furnaces are employed, with each one using different technology.
Foundries construct the melting furnace in a specific way that uses the least amount of heat and fuel to melt the metal. Do you want to know how metal melting furnaces work and the different types of melting furnaces? Then, scroll down this guide.
Explaining The Working Of Metal Melting Furnace
Melting furnaces are utilized to liquefy solid materials by overheating them. Thermal processing appliances are frequently employed to change the surface or susbstances’ interior properties by raising their temperature. It often improves ductility at the price of both hardness and strength in metals.
It necessitates an industrial furnace capable of producing and maintaining temperatures that are less than the melting point of the substance. On the other hand, a melting furnace generates overheated temperatures that surpass the metal’s melting point, resulting in structural breakdown and liquefaction.
The phase change actually relies on pressure and temperature. However, there are some metals that can still stay in a liquid phase where we can exempt the case of mercury (Hg) and recognized eutectics such as gallium-based (Ga-) alloys.
The melting furnace needs to generate and maintain the required temperatures for a long time in order to achieve a homogeneous molten mixture. This procedure can be carried out by a variety of melting furnace layouts. You can check out www.dawangcasting.com to know more about the melting furnaces and different types of melting furnaces.
What Are Different Types Of Foundry Melting Furnaces
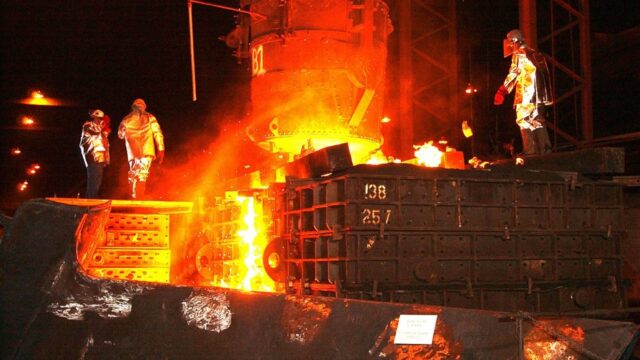
Cupola and crucible furnaces were once the most frequent methods of forging metals for casting. However, as of now, electric arc and induction furnaces have become more common.
Crucible Furnaces
The most basic type of metal furnace is the crucible furnace. The crucible is a container constructed of ceramic or another refractory substance that can withstand extremely high temperatures. The metal and additives are charged into the crucible. Jewelry manufacturers, a few non-ferrous foundries, and some individuals still use crucible furnaces in the present period.
Crucibles are accessible in tiny sizes, like a small cup where metals are dissolved using a blowtorch. In addition, they are also available in enormous containers holding 50 pounds of the substance. Huge crucibles are frequently placed within a kiln-like furnace and pulled out for pouring or material ladled from the top.
Cupola Furnaces
Cupola furnaces are tall, chimney-like structures that contain coal, coke, and other additions. The cupola’s fuel is lit, and once the furnace is hot enough, pig and scrap iron are put in directly. Different classes of iron and steel are generated by dissolving iron around coke and additions, which gives carbon and other components.
You have to remember that cupola furnaces are no longer utilized in manufacturing because electric arc and induction processes are more productive at creating the essential heat. In a few areas, foundry workers toss molten iron against a wall to create dramatic sparks. Due to tradition, they still keep using the cupola furnaces.
Electric Arc Furnaces
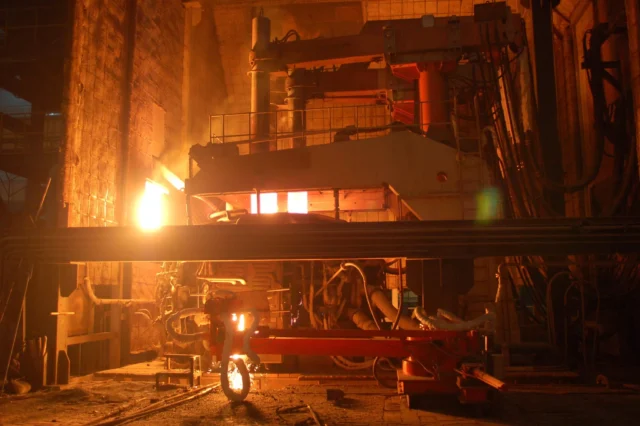
Electric Arc Furnaces (EAFs) first appeared in the late 1800s. When melting large amounts of metal at once, electrodes move electrical current through the metal found inside the furnace, which is more beneficial than adding outside heat. The capacity of a massive EAF utilized in steel production is 400 tonnes.
Gigantic iron slabs and beams, minced junk from vehicles, and pig iron ingots from the smelter are commonly used to make a “charge” of this steel. Electrodes are inserted into the metal once the tank has been replenished and a curve of electricity travels between them.
In order to build a large arc, the electrodes can be dragged further into the mix or split up as the metal melts. It is better to add oxygen and heat to speed up the procedure. The voltage can be increased when molten metal begins to develop since the slag formed on top of the metal functions as a shield covering for the roof and various EAF parts.
When the entire furnace has melted, it is tilted to release the liquid metal into a ladle under it. Often, the ladles themselves are tiny EAF furnaces that maintain the metal hot prior to pouring.
Induction Furnaces
Instead of using electrical arcs, induction furnaces use magnetic fields. A powerful electromagnet composed of coiled copper is used to charge metal into a crucible. When the induction furnace is activated, an alternating current is inaugurated into the coil, which develops a quickly reversing magnetic field.
The magnetic build whirls within the fluid as the metal melts, which self-stir the substance. An induction furnace generates heat by exciting the molecules in the iron itself, which implies that what moves into the crucible will come out as it is. In addition to that, no oxygen or other gases are added to the system.
Since there are fewer variables to manage during melting, an induction furnace cannot be utilized to refine steel. What goes in must also come out. Induction furnaces also release by bending into ladles. When provided high-quality input, induction furnaces are straightforward to operate. Each charge can create 65 tonnes of steel in most variants.
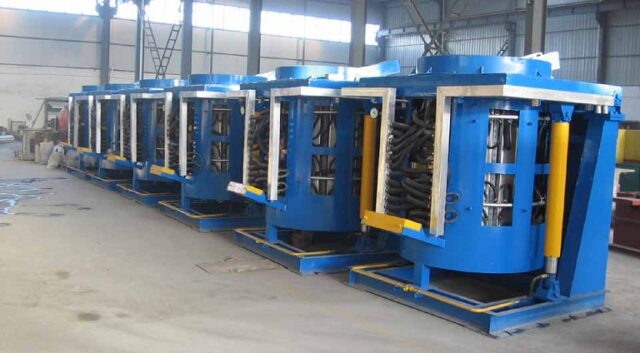
Thin metal pieces bulge out from a filthy induction metal furnace, and they are rusty and scorched. This induction furnace is open and may be charged with metal while still hot. Steam is a deadly opponent for all furnaces on the foundry floor. Since even tiny amounts of water might create squirting or explosions, all trash, ferroalloys, and tools used in manufacturing have to be totally dry before use.
Bottom Line
With the above-mentioned information, it is clear how the metal furnace works. Even though there are different types of metal furnaces, only a few types are used presently. Traditional furnaces used to be popular in the past, but now they are employed in only a few areas or not used at all.