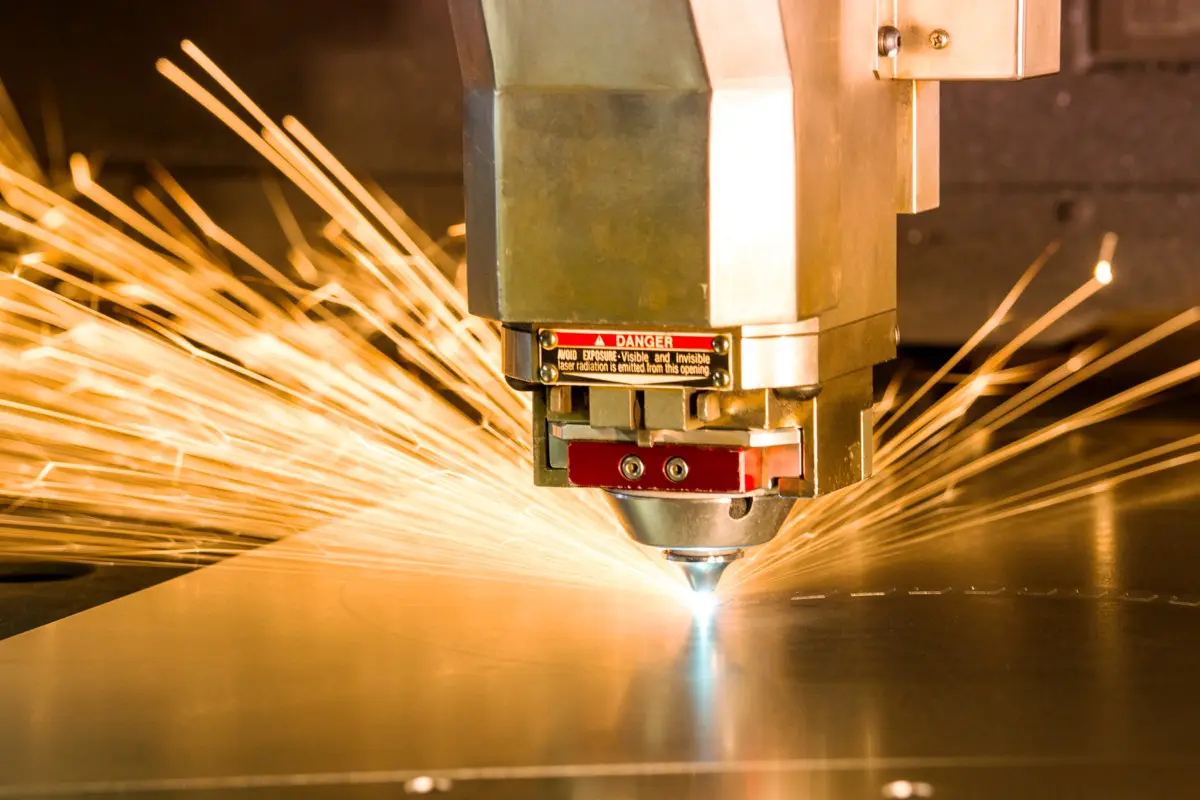
Advancements in industrial processes often come down to precision and efficiency. In the world of metal fabrication, accurate cuts with minimal waste save both time and costs. Nitrogen gas has emerged as a critical element in improving laser-cutting processes by offering cleaner cuts and enhancing overall productivity. Nitrogen generators are instrumental in this process, creating an environment that boosts both the quality and speed of production.
Here’s how they play an essential role in optimizing your laser-cutting setup.
Key Points:
- Nitrogen generators supply high-quality gas for optimal cutting results.
- A clean gas flow improves precision by minimizing oxidation.
- Cost savings arise through an uninterrupted gas supply.
- Nitrogen enhances laser-cutting efficiency by maintaining ideal cutting conditions.
- Long-term use reduces the need for gas cylinders.
Efficiency: Boosting Productivity with On-Site Gas Supply
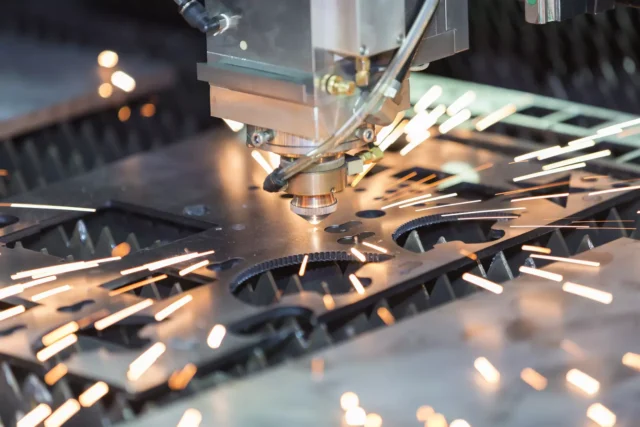
Efficiency defines the success of any manufacturing process. Nitrogen generator laser cutting helps streamline operations. By offering a steady flow of high-purity nitrogen, production cycles are not disrupted. There is no need to stop for cylinder replacements or deal with unpredictable delays in gas supply deliveries. The process becomes smooth, with fewer interruptions.
Companies like Berg Gasetech have specialized in designing nitrogen generator laser cutting tailored applications. Their technology is engineered to optimize gas production, ensuring that the flow remains uninterrupted, which in turn maximizes the operational efficiency of your system. By having the generator on-site, you minimize downtime, allowing your laser machines to work without breaks.
If a fabrication shop wants to remain competitive, the importance of uninterrupted production cannot be overstated. When processes run without delays, it leads to faster turnaround times for client orders, a direct boost to profitability.
Precision: A Core Requirement in Laser Cutting
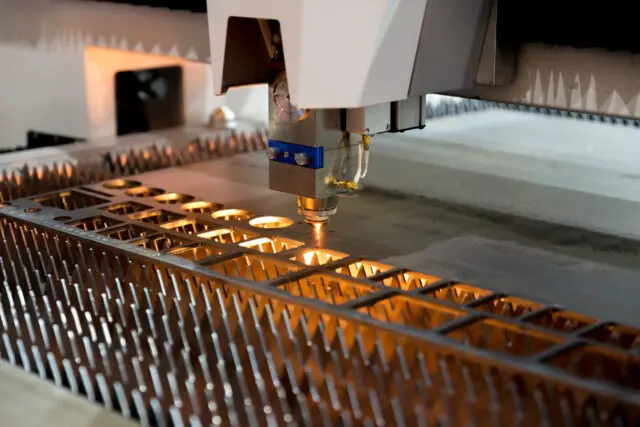
Precision is a non-negotiable element when it comes to laser cutting. The entire process relies on the purity of the gas used. Nitrogen serves as an inert gas, preventing oxidation on metal surfaces. This clean-cutting environment leads to sharp, smooth edges without discoloration or rough patches. It’s here that nitrogen generators come into play. They supply the gas needed to create a perfect cutting condition. Without a consistent supply of nitrogen, precision decreases, and imperfections begin to appear.
The role of nitrogen in cutting processes isn’t just theoretical; it shows in real-world results. When manufacturers integrate an on-site nitrogen generator, they instantly notice an improvement in the quality of the cuts. The generator eliminates the need to depend on external supplies, which can fluctuate in quality and availability. A stable supply means a consistent output, and in metalwork, consistency is the key to success.
Cost Savings: Eliminating the Need for Bottled Nitrogen
When companies switch to an on-site nitrogen generator, they see a noticeable decrease in operational costs. With no need for bottled nitrogen, businesses eliminate delivery fees, cylinder rentals, and the costs associated with handling and storing gas containers.
An on-site generator brings added peace of mind. It removes the unpredictability of external suppliers, who may face shortages or price fluctuations. You control your gas production, knowing exactly what to expect in terms of cost. Once installed, nitrogen generators pay for themselves by significantly reducing the expenses tied to external nitrogen sources.
It’s not just about saving money. Reducing the dependency on third-party suppliers allows companies to focus more on production quality and client satisfaction. There are fewer logistical hurdles, making the entire operation more efficient.
Clean Edges and Improved Aesthetics
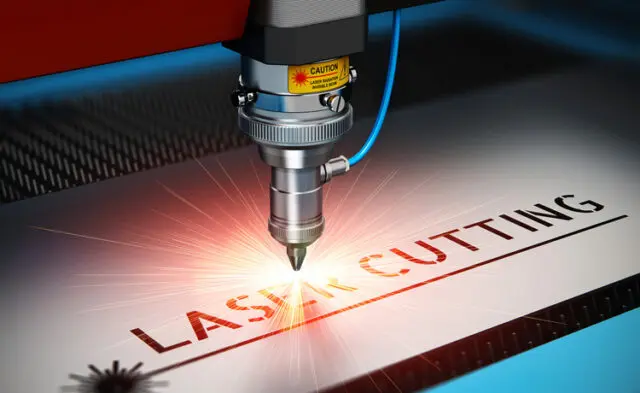
One of the most visible benefits of using nitrogen in cutting processes is the quality of the finished product. By creating an oxygen-free environment during the cutting process, nitrogen prevents any oxidation, resulting in cleaner edges and a smoother finish. When oxidation happens, the result is a discolored or uneven cut, which may require additional work like polishing or sanding.
On-site nitrogen generators ensure that the supply of high-quality gas is always available, allowing you to avoid oxidation consistently. This cleaner, more precise cutting environment leads to products that meet higher aesthetic standards. This is particularly important for industries where appearance plays a critical role, such as automotive or architectural fabrication. The last thing you want is to produce parts that need reworking or extra finishing.
Improving Safety and Environmental Impact
Handling large nitrogen cylinders comes with its own risks, including storage hazards and the risk of leaks. By installing nitrogen generators, these risks are reduced. There’s no need for high-pressure tanks, which means your workers operate in a safer environment.
On top of that, moving away from gas cylinders contributes to a smaller environmental footprint. Gas deliveries result in increased transportation emissions, and gas cylinders themselves are not always recyclable. Producing nitrogen on-site reduces the environmental impact, a factor many companies are now considering in their drive toward more sustainable operations.
Reducing Maintenance Needs
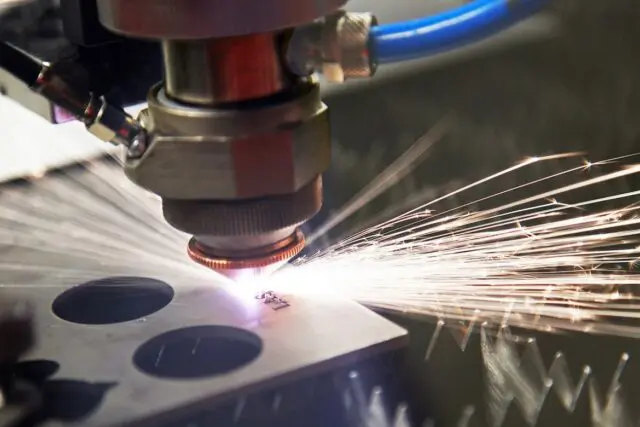
Cutting operations rely on precision, but also on the smooth operation of equipment. By using on-site gas production, there is less wear and tear on your machines. External gas sources can introduce impurities, leading to damage over time. A dedicated nitrogen generator reduces this risk by providing high-quality, clean gas that extends the life of your equipment.
Longer machine life means fewer breakdowns and less need for repairs. When your laser machine works efficiently and requires minimal maintenance, it further reduces downtime and operating costs. It’s a win-win scenario where you’re cutting better and extending the life of your equipment at the same time.
Real-World Benefits for Metal Fabricators
For metal fabricators who deal with high demand and tight deadlines, the ability to produce high-quality work quickly can make or break their business. Nitrogen generators help deliver that high-quality output, ensuring every cut is as precise as possible. They eliminate the potential for delays due to gas supply shortages, and they help to lower overall operating costs.
Many manufacturers see immediate benefits once they install nitrogen generators. Their ability to maintain a consistent level of production, without the need for external nitrogen, leads to faster deliveries and happier clients. Investing in an on-site generator provides a return on investment that stretches beyond cost savings, into areas like improved customer satisfaction and higher product quality.
Conclusion
Nitrogen generators have become an essential tool for any business that relies on laser cutting. Their ability to ensure a clean, efficient cutting environment, free from oxidation and interruptions, gives manufacturers the edge they need in a competitive market. On-site nitrogen production eliminates dependency on external suppliers and provides significant cost savings over time.
For any manufacturer looking to enhance the precision and efficiency of their operations, an investment in a nitrogen generator is a smart move. It improves both the quality of the work and the bottom line, helping businesses stay ahead in the fast-paced world of metal fabrication.
In conclusion, nitrogen generators enhance laser cutting precision and efficiency in significant ways. They improve the quality of cuts, reduce costs, and make production processes safer and more reliable. The benefits go beyond the immediate savings, impacting the long-term sustainability of any operation.