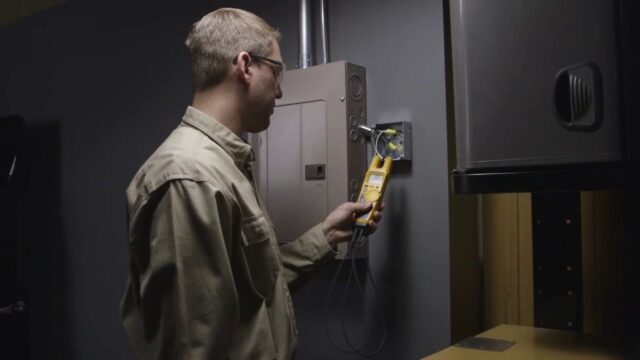
PAT test is not as simple as it seems. Mistakes can happen to anyone. Even seasoned professionals conducting this test for years tend to commit mistakes. So, if you have committed a mistake while testing, you should know that you are not the only one who has done it.
Apart from that, there can be times when you need to be made aware of the kinds of errors that you tend to commit. They can cause issues in the overall process so the results will be unreliable and appropriate.
The best way to avoid such PAT testing mistakes is to have an idea about them and ensure that you avoid falling into the same pit.
Here are some common mistakes you should beware of while PAT testing.
1. The Incorrect Testing Order
The first and most common mistake is that the test order must be corrected. It is a random mistake and can happen to anyone on board. When the tester checks the Class I appliances, there is a need to prove that the conductive earth path is good.
It should be ensured before the process of running the isolation test begins. The results will only be true if you are doing this thing.
Hence, you should ensure that you are ensuring the right test order. And, if you are not doing it, the reliance on the test results will reduce.
2. Not Seeing The Functioning Of The Appliance
The reliance on the insulation test result depends on whether you are switching the appliance under the testing angle or not. If you are not doing it, the results won’t be trustworthy.
It is because the voltage will not pass through the live wires in a switched-off device. The result can be an incorrect pass of any dangerous appliance in a productive environment.
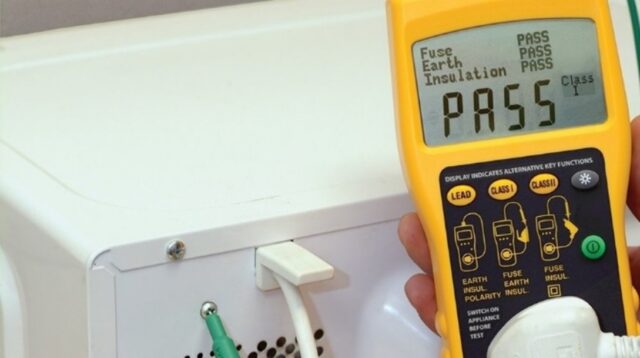
Let’s take an example to understand it. If the live wire within the testing appliance is broken and you touch the outer casing, voltage detection won’t be possible. So, you will have to switch on the appliance for the testing process.
You should note that the insulation tests work through the detecting process with the help of a probe or an earth wire. You need not worry if the voltage is escaping the appliance’s housing. Also, when you are testing, the appliance should be at 500V.
3. Not Paying Attention To The Fuse
If you forget to switch on the appliance, it will directly impact the fuse. It means that you cannot decide whether the fuse is functioning correctly or not, and for that matter, whether the fuse is working.
Also, there is no need for you to perform a separate fuse test to check the conduction. A simple operation test will confirm that the appliance is switched on and the fuse is working perfectly.
4. Too Much Appliance Touching
When you hold an appliance when the insulation testing is going on, you tend to identify the room for improving the probe contact. But it is a bad habit, and you should avoid indulging in it.
The main reason behind this is that amongst all the appliances that you think of testing, there will be many appliances that will pass the insulation test. Eventually, you will get your hands on the one that fails. Also, if you are holding the appliance during this time, you can suffer from an electric shock.
5. Doing Only A Single Earth Bond Test
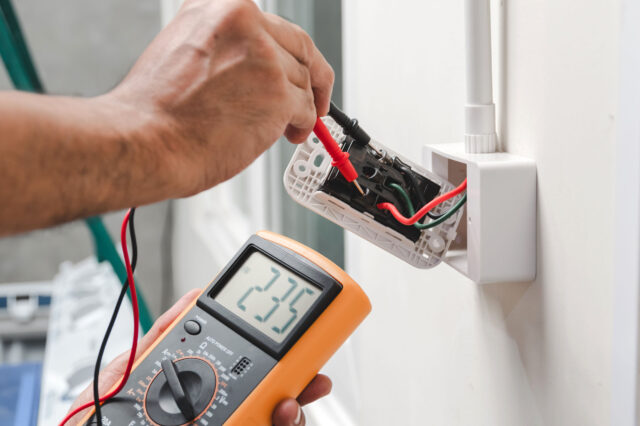
During the earlier times, many PAT testers used to offer a standard testing sequence and used to move forward with a single earth test. The result of this step is that even experienced professionals used to fall into the trap of conducting a single earth test.
However, if an appliance has more than one isolated outer part followed by separate earth parts, it is mandatory to test each.
6. Not Marking The Correct Readings
All the appliances may not have a single reading. Many appliances with multiple parts show different parts of the reading. The parts can be isolated and will have separate earth parts.
Hence, a single bond test will not do any good. Also, the testing will only give you the desired results if you take the average reading. And if you are doing it, the results will only be worse.
7. Performing A Single Insulation Test
Many professional testers go for the standard test sequences with a single insulation test. But, the testers need to know that there are different appliances where the insulation degrades.
For example, the insulation will break down around the ventilation slots, chucks, triggers, and other areas like the assembly screws. Hence, going for a second insulation test at all costs is important.
8. Not Performing The Operation Test
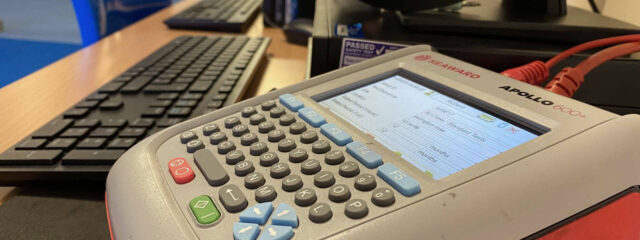
As beginners, many PAT testers have admitted to making this mistake. They cannot power up the appliances, so they don’t consider doing an operation test. When such a situation occurs, you must ensure the appliance works correctly.
You can know it by plugging it into a socket after conducting the PAT test and after the power is on.
9. Conducting The Tests On Class II Appliances
This is another problem that occurs commonly. If you attempt the test on any Class II appliance, the results are nothing less than a failure. The results will be such because this family of appliances doesn’t have an earth.
10. Forgetting The Visual Inspections
The first step of a PAT test is to conduct a visual inspection. If you don’t do it, moving forward is no use. You will be surprised to know that 90% of the faults can be solved when you do a careful visual inspection.
But, if you increase your reliance on the tester, there is a higher chance that these faults will be missed, and they will create issues later on.
Conclusion
PAT testing mistakes are common, but this does not mean you can freely commit them. If you ignore these things, the issues will increase, reducing the tests’ efficiency and results.
Hence, you should discuss them beforehand so there are fewer problems in the later stages.