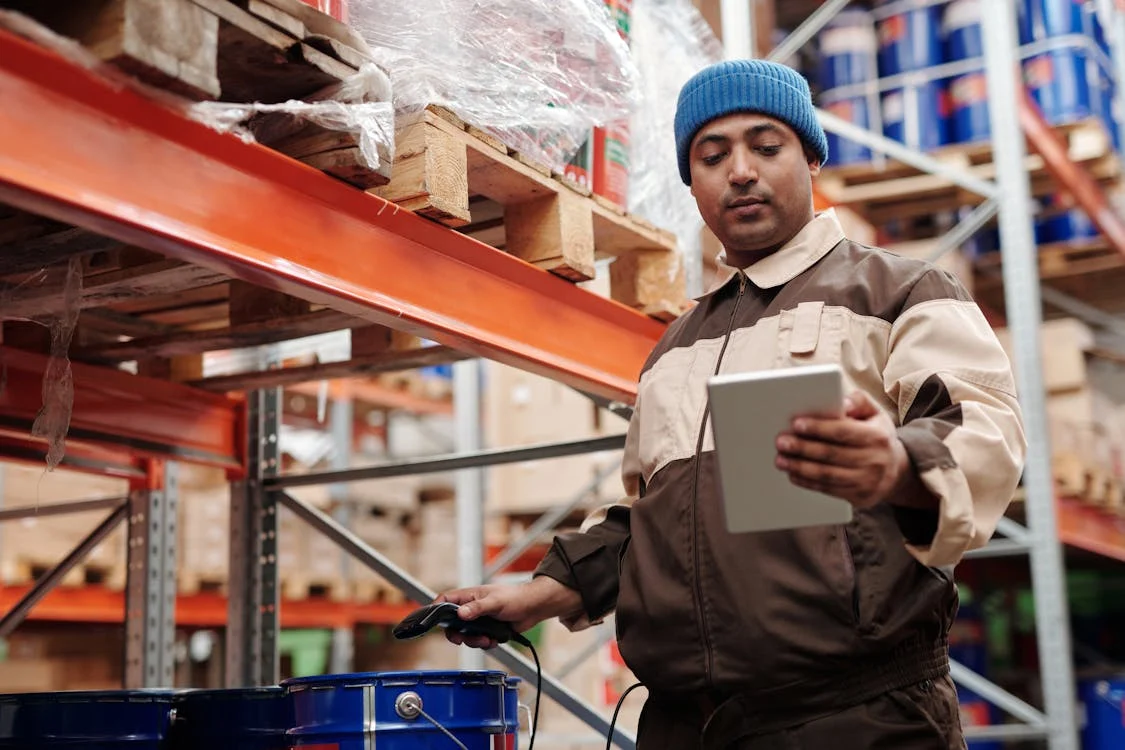
Small warehouses face unique challenges when it comes to storage and handling. Unlike larger facilities, space constraints can significantly impact efficiency, organization, and ultimately, profitability. This article explores practical strategies to address these challenges, ensuring that small warehouses operate at their full potential. For more insights, visit https://lenokers.com/.
Maximizing Storage Space
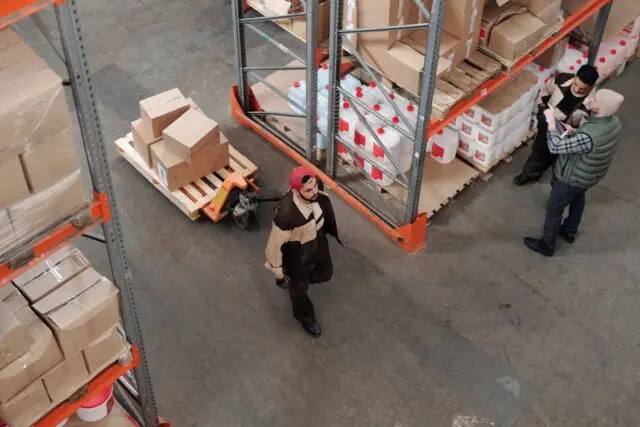
One of the biggest challenges in small warehouses is the limited storage space. To tackle this, you need to think creatively and strategically about how to use every inch of space.
Vertical Storage
When floor space is at a premium, the only direction left to expand is up. Utilizing vertical space effectively can significantly increase your storage capacity. Consider installing tall shelving units or racks that allow you to store items all the way up to the ceiling.
- Adjustable Shelving: This allows you to customize the height of each shelf according to the size of the items being stored. Adjustable shelves can help maximize the number of products stored in a vertical space.
- Stackable Bins and Pallets: Use bins and pallets that can be safely stacked on top of each other to save floor space. Ensure that the stacking is stable to avoid accidents.
Strategic Layout Planning
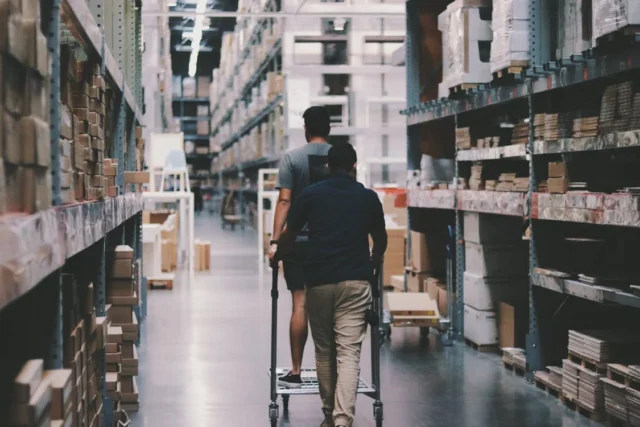
The layout of your warehouse plays a crucial role in how effectively you can use the available space. A well-planned layout can make the difference between a cramped, disorganized warehouse and a smooth, efficient operation.
Zone Your Warehouse
Divide your warehouse into distinct zones based on the type of activity that takes place in each area. For example, create separate zones for receiving, storage, packing, and shipping. This reduces unnecessary movement and makes the workflow more efficient.
Narrow Aisles
Consider narrowing the width of aisles to maximize storage space. However, ensure that they are still wide enough for safe and efficient movement of goods and equipment.
Cross-Docking
Implement cross-docking practices where possible. This involves unloading incoming goods directly into outbound vehicles, minimizing the need for storage space.
Improving Inventory Management
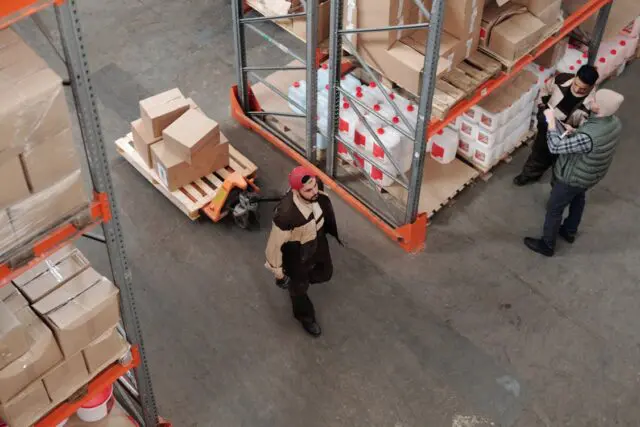
Efficient inventory management is crucial in a small warehouse, where space is limited, and mistakes can be costly. Even without advanced technology, there are effective strategies to keep your inventory under control.
Just-In-Time Inventory
- Adopting a Just-In-Time (JIT) inventory system can help reduce the amount of space needed for storage. JIT involves receiving goods only when they are needed for production or sale, rather than storing large quantities of stock.
- Supplier Relationships: To successfully implement JIT, build strong relationships with suppliers who can deliver products quickly and reliably as needed.
- Regular Inventory Audits: Conduct regular audits to ensure that stock levels are accurate and that you are not holding onto more inventory than necessary.
First-In, First-Out (FIFO) System
Using the First-In, First-Out (FIFO) method ensures that older inventory is used or sold before newer stock. This reduces the risk of items becoming obsolete or expired, which is particularly important in small warehouses where space is at a premium.
Label all stock with the date it was received and organize it so that older items are easy to access and use first.
Optimizing Stock Levels
Stock levels should be optimized to ensure that you are not overstocked or understocked. Overstocking can lead to wasted space, while understocking can result in delays and missed opportunities.
Use past sales data and market trends to predict future demand and adjust your stock levels accordingly. Set minimum order quantities with suppliers to avoid ordering more stock than you can efficiently store.
Streamlining Material Handling
Handling materials efficiently is essential in a small warehouse, where space is limited, and every movement counts. By optimizing how you handle goods, you can reduce waste, improve productivity, and maintain a safe environment.
Choosing the Right Equipment
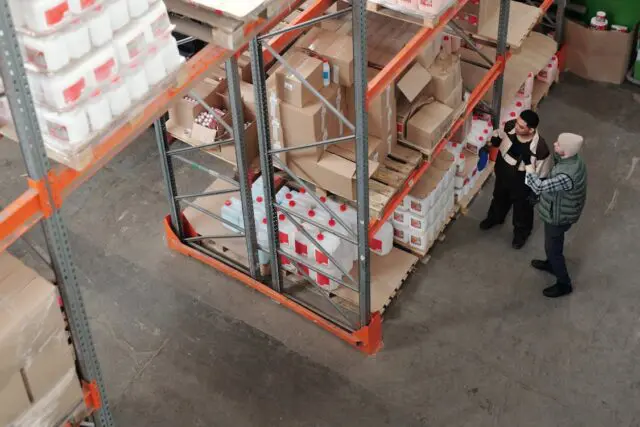
Selecting the right material handling equipment is crucial for maintaining efficiency in a small warehouse. The wrong equipment can lead to bottlenecks, accidents, and wasted space.
- Pallet Jacks Over Forklifts: In tight spaces, pallet jacks are often more suitable than forklifts. They are smaller, easier to maneuver, and can still handle significant loads.
- Hand Trucks: For moving smaller loads, hand trucks are a versatile and space-saving option. They allow for easy movement of goods without taking up much space.
- Rolling Ladders: If you’ve implemented vertical storage, rolling ladders provide safe and easy access to high shelves without taking up permanent floor space.
Workflow Efficiency
Improving workflow efficiency is vital for small warehouses. A streamlined workflow minimizes unnecessary movement and reduces the risk of errors and delays.
Designated Work Areas
Assign specific tasks to designated areas within the warehouse. For example, have a dedicated area for packing and another for shipping. This reduces confusion and ensures that everything is done in an orderly manner.
Clear Signage
Use clear signage to guide employees through the warehouse. Mark zones, aisles, and specific areas to avoid confusion and ensure a smooth flow of goods.
Enhancing Safety in Small Warehouses
Safety is a critical concern in small warehouses, where tight spaces can increase the risk of accidents. Implementing effective safety measures is essential to protect employees and maintain a smooth operation.
Regular Safety Inspections
Conduct regular safety inspections to identify potential hazards in the warehouse. These inspections should focus on the layout, handling equipment, and storage methods.
- Aisle Safety: Ensure that aisles are clear of obstructions and that there is enough space for employees to move safely.
- Storage Safety: Properly secure items on shelves to prevent them from falling, especially in vertical storage setups.
Equipment Maintenance: Regularly inspect and maintain handling equipment to ensure it is in good working condition and safe to use.
Ergonomics
Ergonomics is essential in preventing injuries and ensuring that employees can work efficiently in a small warehouse environment.
Design workstations to minimize strain and encourage proper posture. Adjustable work surfaces and anti-fatigue mats can make a significant difference in employee comfort and productivity.
Train employees on proper lifting techniques to prevent injuries. In a small warehouse, where space is tight, lifting incorrectly can easily lead to accidents.
Emergency Preparedness
- Prepare for emergencies by establishing clear procedures and ensuring that all employees are trained on them.
- Emergency Exits: Clearly mark all emergency exits and ensure they are free of obstructions at all times.
- First-Aid Training: Provide employees with basic first-aid training so they can respond effectively to injuries or accidents.
Conclusion
By maximizing storage space, optimizing inventory management, streamlining material handling, and enhancing safety, small warehouses can operate efficiently and effectively. It’s important to remember that small changes can have a big impact in a small warehouse.